FCU - Fuel Cell Control Unit
Introduction
Fuel Cell Engine (FCE) is a complex, multidisciplinary system, as the control unit for FCEs, FCU needs to have strong computing and processing capabilities and rich collections of I/O to effectively manage and coordinate various of subsystems, to ensure the safe and strong power generation from the battery system for prolonged period of time.
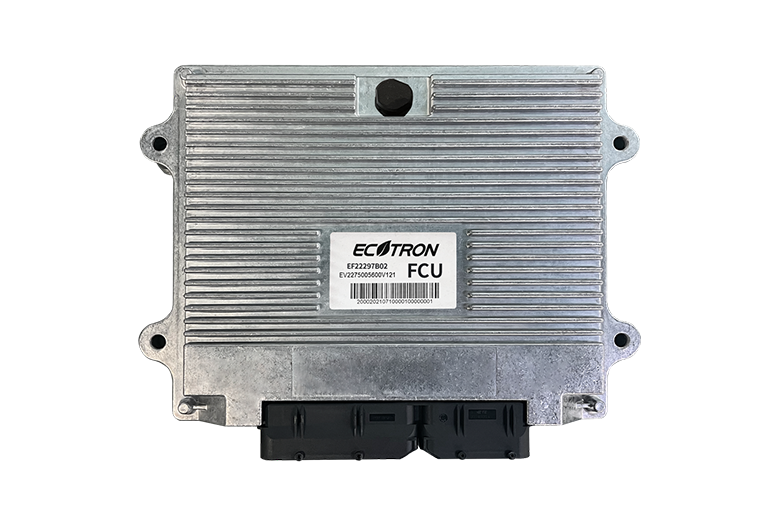
Features:
- Based on the automotive grade 32-bit MCU Infineon AURIX™ series TC27xT platform, withmulti-core architecture.
- The design and development of software, hardware, and control strategy comply with ISO26262 functional safety requirements. With a built-in safety monitoring chip, our FCU is ASIL-D rated.
- Built-in basic software (BSW) supports automatic code generation tool EcoCoder (rapid prototyping), and all popular input/output of a typical fuel cell system. BSW is packaged in the MATLAB/Simulink environment, and users can develop control strategies with 100% model-based design methods.
- Equipped with a CAN bus-based software flashing tool, which is guided by the bootloader flashed into the microcontroller in advance.
- Gas path management: Precise control of the hydrogen flow, airflow, pressure, humidity, and temperature required by the fuel cell system.
- Water and heat management: Precise control and adjustment of the circulation, heating, heat dissipation, air temperature, cooling water temperature to improve the power efficiency and reliability of the fuel cell system.
- Electrical management: Monitoring the battery pile voltage and current, adjust the output power, and control the fuel voltage within a reasonable range, manage the residual power, and provide the voltage and current protection.
- Data communication: Communicating with other subsystems, interchange important data and control signals.
- Fault diagnosis: Capable of perform fault diagnosis, raise warning, and initiate protection routine for various subsystems.
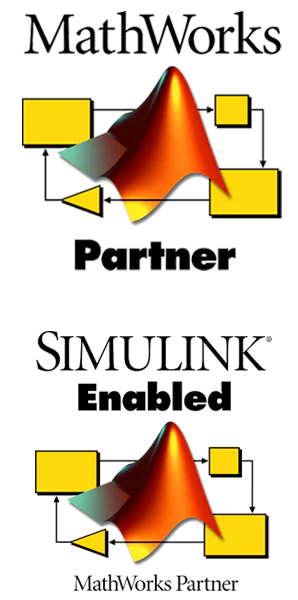
